How to Manage Inventory Across Multiple Locations?
Multi-location inventory management can feel like balancing on a tightrope. It seems simple in theory–just keep track of inventory, ensure everything is in the right place, and you’re done. But in reality, it’s much more complex.
You have to deal with changing customer demand, make sure popular items are always in stock, and handle many other tasks. The risks are significant, poor inventory management can upset customers, increase costs, and cause a lot of stress.
However, there’s good news: with a solid plan and the right tools, multi-location inventory management doesn’t have to be overwhelming.
This guide will explain everything, from the “why’’ behind effective inventory management to the “how’’ of getting it done like a pro.
:format(webp)/https%3A%2F%2Fbrandsgateway.com%2Fapp%2Fuploads%2F2024%2F06%2Fbanner.jpg)
Looking for a reliable dropshipping or wholesale supplier?
Join us today for top-quality products and unbeatable prices.
What is multi-location inventory management?
Multi-location inventory management is the process of tracking and managing inventory across multiple stores, warehouses, or locations.
It ensures that stock is properly distributed, and businesses can keep track of inventory levels in different places to meet customer demand efficiently.
Why use multi-location inventory management?
If your business has several locations, like warehouses, stores, or regional centers, managing inventory well is very important.
Properly spread-out stock helps you quickly fill orders, making customers happy with fast deliveries that make them loyal. It also saves money by preventing too much stock in one place and not enough in another, cutting down on extra shipping costs.
A good inventory system also makes your business more flexible, allowing you to confidently grow when you open new stores or enter new areas.
For instance, if you don’t manage inventory well, one store might run out of items while another has too many unsold things, causing lost sales and higher costs.
By keeping stock balanced across all storage locations, you can avoid these problems and keep both your business and customers happy.
How to set up a multi-location inventory management system?
Handling inventory in different places can be tricky, but with good methods, you can make things smoother and more efficient.
Here are important ways to improve how you manage inventory in multiple places.
Distribute stock based on demand across locations
When dealing with inventory in various locations, it’s important to spread out your stock based on what each area needs.
By looking at past sales data from each place, you can see what sells well and adjust how much stock you keep in each warehouse or store. This helps lower shipping costs and waiting times, making sure products are available where they’re needed most, which makes customers happier.
Optimize layouts for efficiency at all locations
Organize each of your locations to work as efficiently as possible.
Make sure popular items are close to shipping or pickup areas in every warehouse or store, which will speed up order fulfillment. Keep similar products together so staff can find what they need quickly.
Using the same warehouse layout in all locations ensures a smooth and efficient process, whether orders are picked up in-store or shipped from the warehouse.
Use inventory metrics across locations
Keeping track of inventory data across all locations is important for smooth operations.
Watch metrics like stock turnover, out-of-stock items, and order accuracy for each location to spot trends and issues. This data helps you see if some locations have too much or too little stock, allowing you to make better decisions to balance inventory levels, cut costs, and enhance customer satisfaction.
Automate processes across locations
Automation can streamline multi-location inventory management by using warehouse management systems (WMS) or centralized software that tracks inventory across all locations. WMS can automate tasks like stock tracking, order fulfillment, and product transfers between warehouses, ensuring that inventory data is always up to date.
By integrating automated processes across your locations, you can reduce human error, improve accuracy, and make inventory management more efficient, no matter how many locations you operate from.
Define clear roles and responsibilities
Defining clear roles and responsibilities is of big significance when it comes to keeping things running well when managing inventory across multiple locations. Give your team specific jobs, like who checks stock levels, who orders more supplies, and who keeps track of items moving between stores.
When everyone knows their part, they can do their job properly and make sure the inventory is managed well. This avoids misunderstandings and helps everyone take responsibility, which stops mistakes between what’s written down and what’s there.
Standardize procedures
In multi-location inventory management, establishing consistent procedures for receiving new stock, counting of stock, and returns is necessary. This makes sure that all stores follow the same process, hence minimizing discrepancies and increasing accuracy.
Finding a consistent process for all locations will save time and effort while ensuring inventory accuracy.
What are the 4 types of inventory management systems?
With the right approach to managing inventory, you can keep track of your products no matter how many places they’re stored in.
But to do this, you’ll also need to choose the main type of inventory management system you’re planning on using.
Perpetual inventory system
This system constantly monitors inventory in real time. Whenever an item is sold or added, the system instantly adjusts the inventory numbers. These systems usually use barcode scanning or RFID to make the process smoother, cutting down on mistakes and boosting efficiency.
Best for: It works well for businesses with many sales or several locations because it keeps stock levels precise and current.
Periodic inventory system
In this system, inventory is checked only at set times, like weekly, monthly, or yearly. During these times, businesses manually count the stock and update their records. This method is easier and cheaper but can cause inaccuracies between checks.
Best for: Small businesses with low sales volume and fewer SKUs. It’s best for businesses that can handle inventory checks at regular intervals rather than in real-time.
Just-in-time (JIT) inventory system
JIT aims to keep inventory low by ordering items only when they’re needed. This helps cut storage costs and ensures that stock matches actual customer demand.
Best for: Retailers with low storage space or those that sell perishable or trendy items. It’s ideal for those aiming to minimize inventory holding costs while ensuring products arrive just in time to meet customer demand.
Economic order quantity (EOQ) system
The EOQ system figures out the best amount of inventory to order, balancing the costs of ordering and storing. It uses a math formula based on demand, ordering costs, and storage costs to find the perfect order size. It helps prevent both overstocking and running out of stock.
Best for: Businesses that sell large quantities of similar items or products with consistent demand.
The role of technology in inventory management
Technology is pretty much one of the most important parts of effective inventory management across multiple locations. With the right tools, businesses can automate tasks, monitor stock levels instantly, and make better decisions that improve overall efficiency.
Here are some important technological tools that are crucial for multi-location inventory management:
Inventory management software
Software like Zoho Inventory makes managing inventory much easier. This kind of platform offers features such as tracking stock across different warehouses or stores in one place.
Detailed analytics give you insights into sales patterns, helping you make smart decisions about inventory levels and product choices.
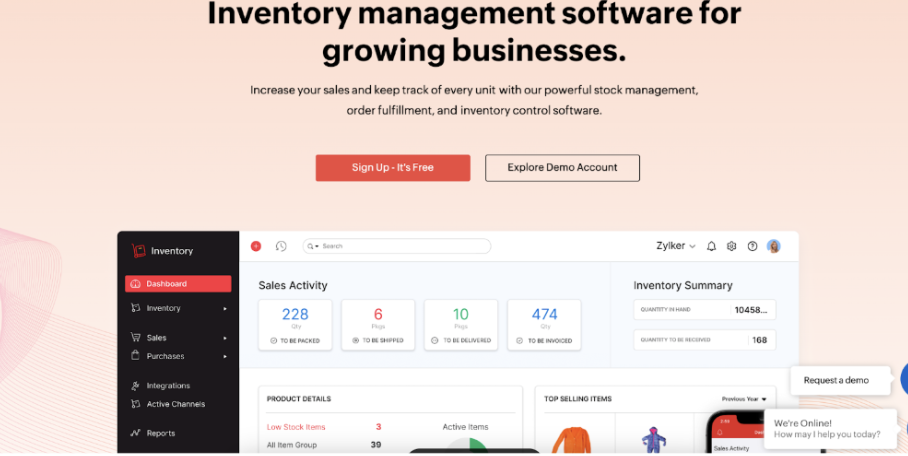
Cloud-based solutions
Cloud-based inventory management systems, like NetSuite, let you check inventory data from any place, which is very useful for companies with remote workers or many locations.
These systems make automatic inventory updates, no matter where your staff is working.
Cloud-based tools also help teams work together better because everyone can see the same real-time data, improving how the company communicates and makes decisions.
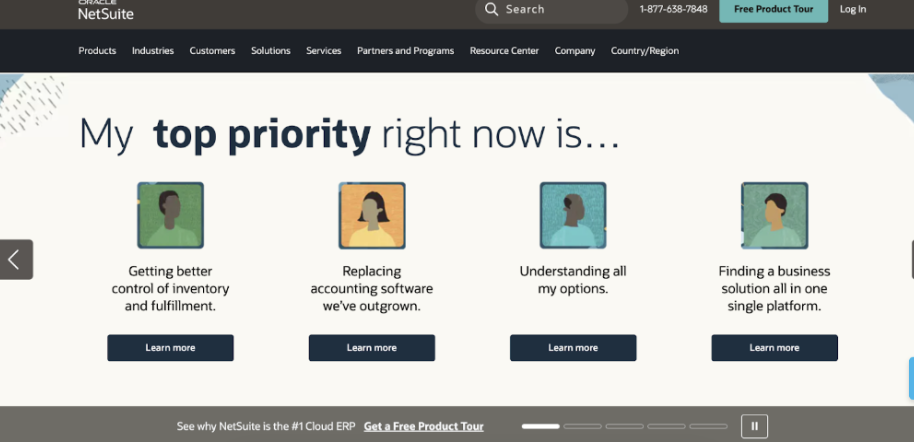
Artificial intelligence (AI) tools
AI-powered inventory management tools, such as Inventory Planner, use sales data to predict what customers will want and to manage stock levels better. By looking at past sales trends, these AI tools can guess future inventory needs, helping businesses avoid having too much or too little stock.
Some AI systems even recommend the best time to move stock between locations, making sure each place has the right amount to meet local demand, which improves overall business efficiency.
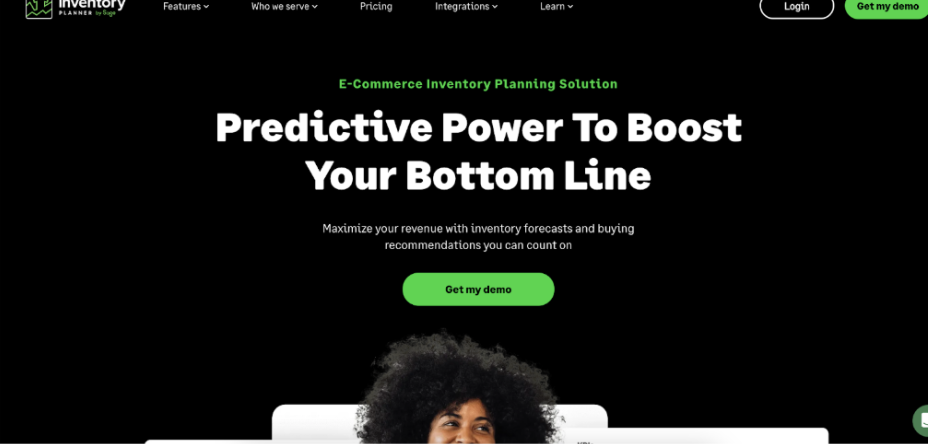
Conclusion
Handling inventory at different locations can be tough, but it’s about setting up a system that works for your business. Begin with a central way to track everything, use technology to help, and be ready to adjust your methods as you figure out what works best.
Once your inventory is well-organized, other things like customer happiness, cost savings, and business growth will naturally follow. Use these ideas, adapt them to your needs, and see your business succeed.
Related articles
Our clients' success stories speak volumes about the impact BrandsGateway has had on their businesses.
View More Articles